Industrial buildings require robust, durable roofing that can withstand the elements and heavy use, often necessitating the expertise of a commercial roofing contractor. Choosing the right commercial roof system is crucial to protecting your structure and minimizing costs over the long run. Several factors, including roof maintenance and inspection requirements, must be considered to select the optimal roof type for your needs.
Assessing Your Building’s Roofing Needs
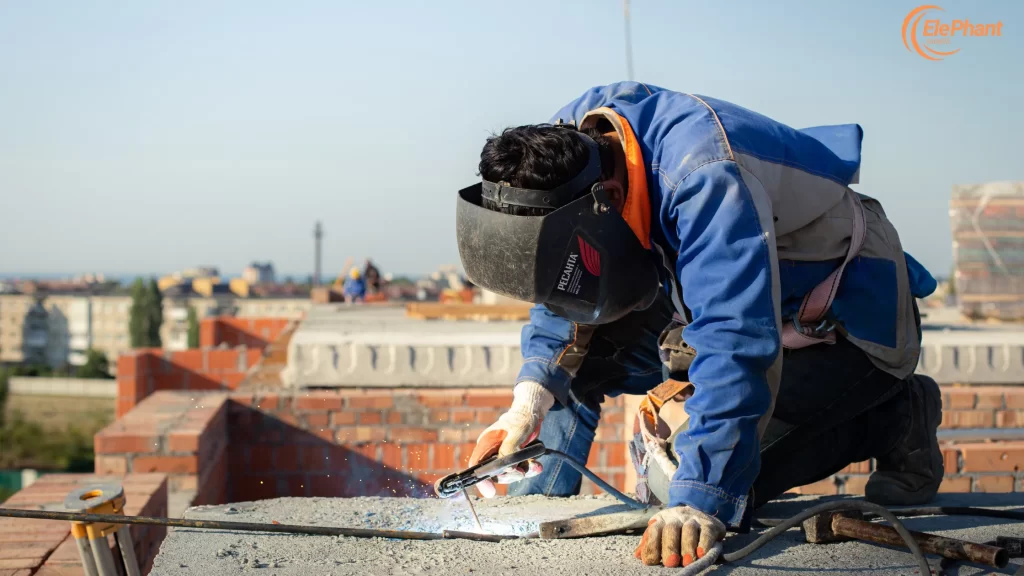
The first step is evaluating your building’s unique conditions and priorities. Consider weather exposure, weight load capacity needs, budget constraints, planned roof lifespan, and environmental impact goals. Inspect the existing roof for damage or issues requiring attention. Document specifications to share with prospective contractors. Understanding these specifics enables narrowing options to products well-suited for the job.
Types of Industrial Roofing Materials
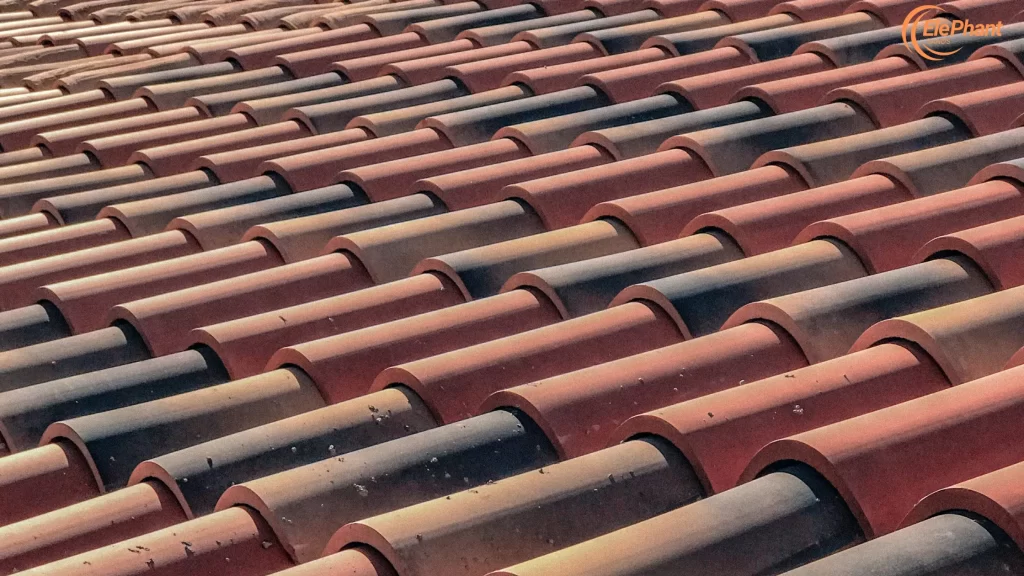
Common industrial roofing materials each have pros and cons depending on circumstances. Built-up roofs incorporate multiple layers of asphalt and gravel for strength but require more maintenance, which should be factored into your roofing services plan. Modified bitumen employs torch-applied membranes for waterproof protection and ease of repair, making it a preferred choice for many roofing companies.
Metal roofing, like standing seam, provides durable weather resistance and is ideal for harsh environments, yet it has a steeper price tag. Thermoplastic polyolefin (TPO) and ethylene propylene diene monomer (EPDM) rubber membranes offer flexibility and longevity at competitive costs if installed correctly by a qualified roofing contractor.
Choosing a Reputable Roofing Contractor
Carefully selecting an experienced, licensed, and insured flat roofing company is vital for a quality result. Request referrals from building owners with similar structures. Interview candidates to assess expertise with industrial roofing projects as well as experience working with flat roofing companies. Consider their positive reviews, warranty offerings, and safety protocols. Comparative estimates help evaluate the value between options. A track record of satisfactory past work, timely completion, and responsiveness to service needs from both industrial flat roofing clients offers reassurance.
Durability and Longevity of Roofing Options
Maximizing the length of time before replacement is required reduces long-term expenses. Factors like thickness, strength of materials, installation quality, roof pitch, and environmental exposure dictate lifespan estimates. Built-up or metal systems tend to endure 20-30 years if properly maintained. Thermoplastic or modified bitumen may degrade more quickly depending on sunlight exposure. Choosing a roof type rated to outlast planned ownership of the building pays off by avoiding future replacement costs.
Energy Efficiency and Insulation
Incorporating insulation reduces heating and cooling demands in an industrial facility. Roofing membranes commonly provide little insulating value themselves. However, adhesives and mechanically attached systems can integrate various R-values of rigid insulation boards into the assembly.
Higher-performing insulations like polyisocyanurate contribute most to energy savings but have a higher upfront cost, making them a consideration for commercial roofing projects. Balancing insulation with budget determines the optimal thermal barrier. Proper ventilation also prevents condensation issues within the roof deck, which is crucial for maintaining the integrity of commercial roofs.
Weather Resistance and Climate Considerations
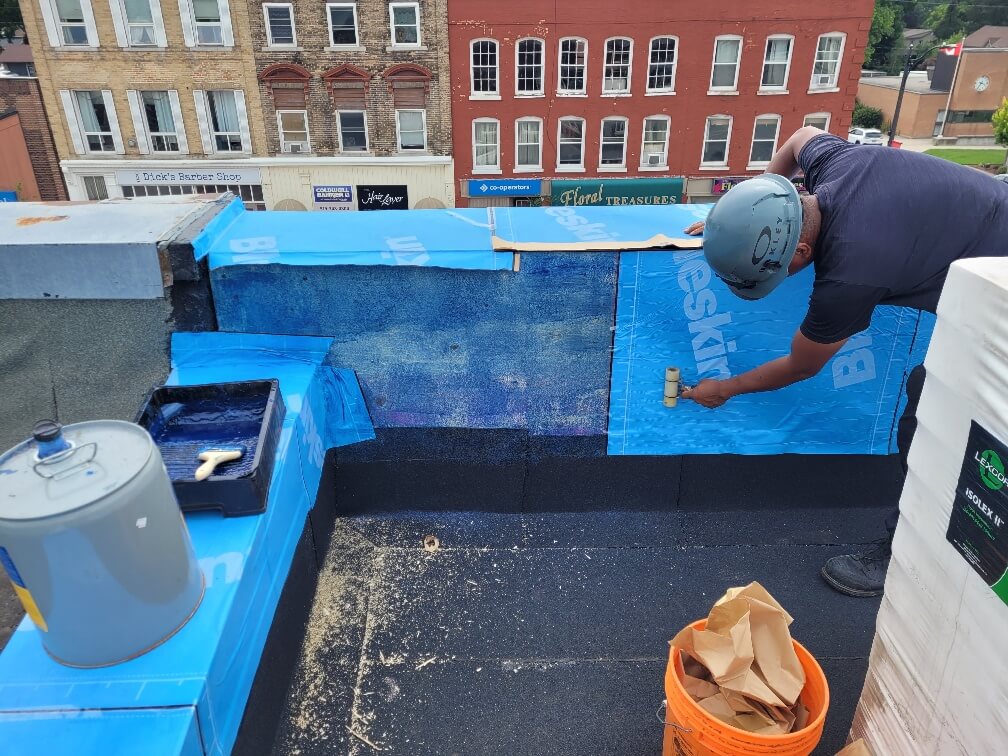
Roof material selection depends highly on the climatic stresses a building experiences, making a thorough roof inspection essential. Harsh snow, wind, and humidity environments require durable options like standing seam metal or thicker membrane systems for commercial and industrial applications.
Hot, dry climates allow for a wider variety of roofing options since moisture is less problematic for commercial roofs. Coastal exposures demand resistance to salt spray and wind-driven rain. Choosing products rated for the roof’s weather zones helps ensure it withstands local conditions without damage or deterioration for decades.
Cost Comparison of Different Roofing Systems
Acquisition and installation costs are significant, yet a roofing company can also address the total cost of ownership factors in maintenance requirements and replacement intervals. In comparison, metal roofs incur higher initial expenses than membranes; their longevity offsets repeated application costs.
Polyurethane foam or comparably performing insulation boards increase material budgets but save substantially on energy costs, making them a popular choice among commercial roofing contractors. Budget-minded decisions should factor in the “life cycle” expense picture rather than just sticker prices, especially when hiring a roofing contractor. Rebates for “green roof” products may also defray some of their premium pricing.
Read More: The Future of Home Energy: Transitioning to Residential Solar Roofing Systems
Maintenance Requirements and Ease of Repair
Low-maintenance roofing eases the financial and time commitments of upkeep. Simple repair of isolated damage prevents costly full replacements. Built-up and metal panels allow spot repairs when punctured leaving no ill effects. Membranes’ single-ply construction means even small tears require partial re-sheets for watertight integrity. Monthly inspections, annual drain cleaning, and repainting of metal seams every 10 years are preventative care duties. Outsourcing maintenance contracts streamlines upkeep responsibilities.
Final Thoughts
- Evaluate building conditions and lifespan plans
- Research appropriate material types for weather, load capacity, and budget
- Thoroughly vet qualified roofing contractors
- Consider insulation value, durability, and total cost over the roof’s lifetime
- Confirm product and installation warranties in writing
- Inspect the roof annually and conduct routine maintenance
That covers the key factors to consider when choosing the optimal industrial roofing system for long-lasting protection adapted to your building’s needs. Selecting the right materials installed correctly by a reputable pro establishes a durable roof prepared to withstand heavy usage and weather for decades.